By Tim Dondero, IW General Manager
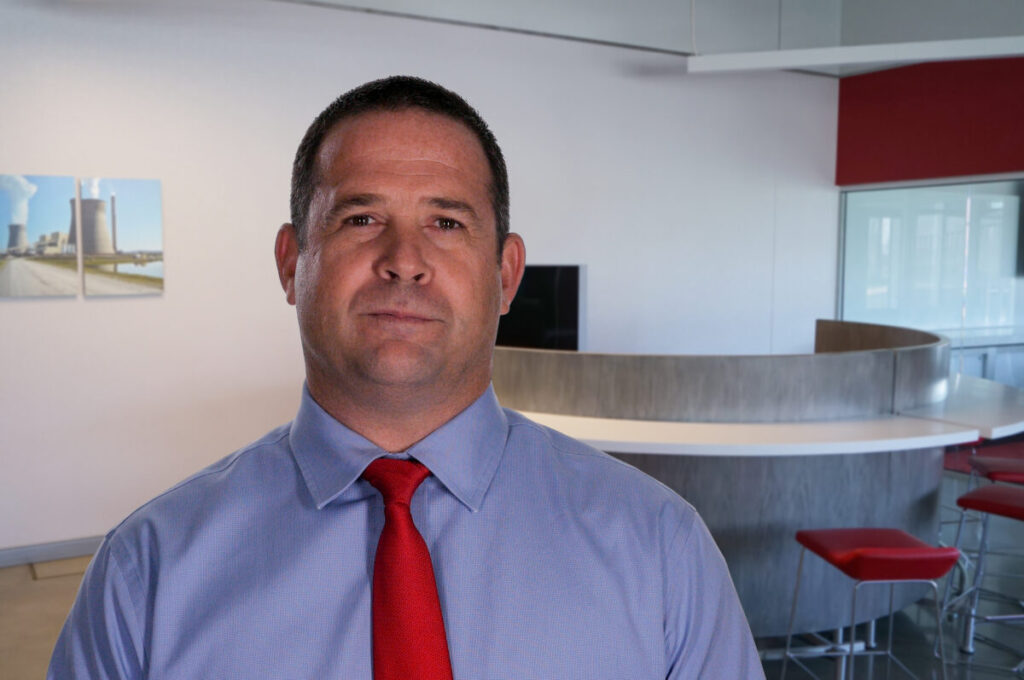
Unprecedented arctic weather plunged Texas into an energy crisis in February, causing severe service challenges for MPW, particularly the Industrial Water Division’s Port Arthur Service Center.
However, MPW has once again proven through its dedication to servicing clients that this team can overcome any obstacle.
In early February, the IW dispatch team anticipated high customer demand for mobile systems, based on the weather forecast in the Gulf Coast. The team began moving trailers from other service centers to Port Arthur, Texas throughout the first week of February.
The Sales team in the area reached out to many of our key customers, alerting them that they should take trailers ahead of the cold spell in case there were weather-related transportation challenges. Some customers heeded this advice, but many did not.
From February 8 to February 18, DI trailers were in extremely high demand throughout the Gulf Coast region. However, many Texas highways were shut down due to weather, making mobile DI delivery impossible. Additionally, many suppliers could not deliver the needed chemicals to Port Arthur.
All of MPW’s other Industrial Water Service Centers (Newark, Ohio; Wilkes-Barre, Pennsylvania; Sedalia, Missouri; Andrews, South Carolina and Yuma, Arizona) supported the Gulf Coast with equipment.
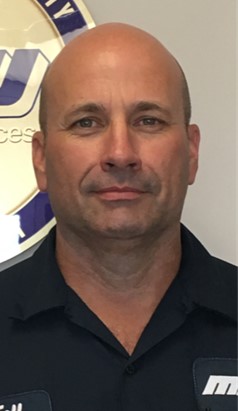
Compounding the problem, the city of Port Arthur experienced significant leaks in its water-distribution lines, which led to our Port Arthur Service Center losing its entire water supply until the damage could be repaired. This process took nearly 10 days. During this time MPW’s Port Arthur Plant Manager, Jeff Hale, coordinated with some local trucking companies to haul water from the Water Department to the MPW facility via 6,000-gallon tanker trucks. This was a slow process, but it allowed the plant to run at approximately 50% capacity. The Port Arthur plant utilizes between 100,000 and 200,000 gallons of water per day when running at full capacity.
Due to the challenges related to the Texas power grid, MPW prioritized power-generation customers during the first few days of the crisis. The IW team communicated with customers’ corporate offices to ensure distribution of DI trailers to their respective plants. During this time, the power pricing in Texas reached $9,000 per kilowatt-hour, which was driven by both low supply and high demand. As a result, many power plants that normally don’t run were trying to help supply the grid while taking advantage of the high pricing. On February 19, pricing dropped to $0.78 per kWh as power was restored to meet demand.
Many of MPW’s loyal customers in the chemical, refining and paper industries were also in need of trailers during this time. Our round-the-clock logistical problem solving allowed us to maintain supply for all our contract customers. Once our contract customers were prioritized, we were able to deliver to some new customers who could not get trailers from our competitors. Some of these companies are still taking trailers from us, even after the crisis.
During this time all the IW Service Centers were busy 24 hours a day. Hale and his team worked with the city of Port Arthur to keep as much water supplied as possible. Rocky Zizzo and the corporate procurement team worked tirelessly to ensure the plant had a supply of hydrochloric acid. When bulk trucks of chemical were unavailable, we sourced totes and the Port Arthur team pumped them into their tank in order to maintain the regeneration process.
The week of February 22, Director of Plant Services Jeff Thornton and Process Manager Brent Hamilton departed from Hebron and Plant Maintenance Technician Hunter McNerney traveled from Yuma to support the Port Arthur plant’s recovery efforts. Thank you to everyone at MPW who helped us deliver this excellent level of service despite extraordinary conditions!