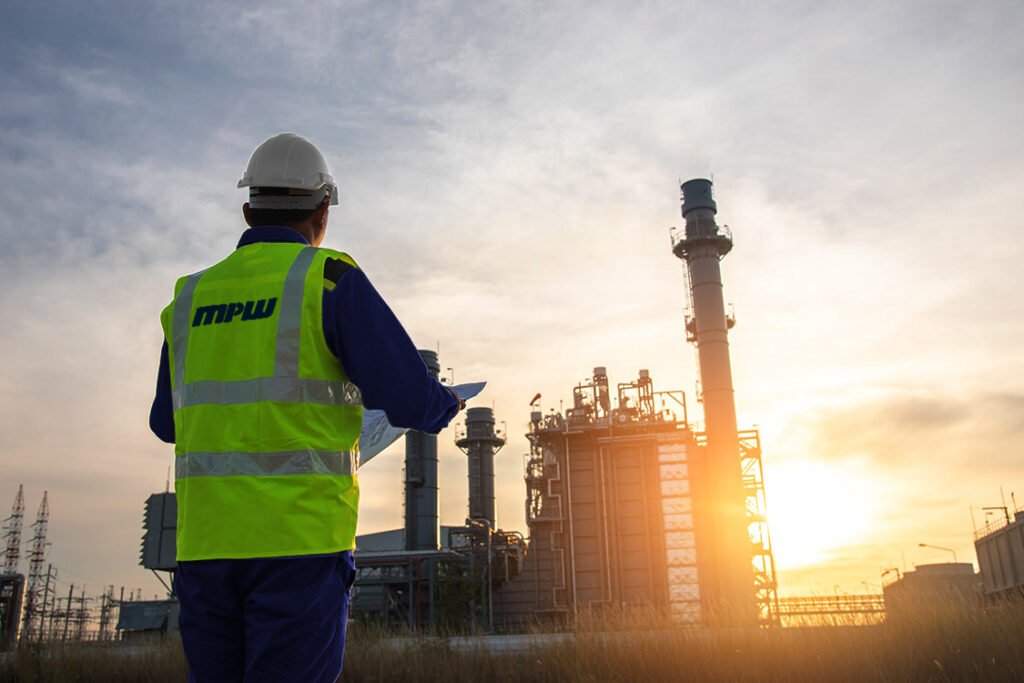
PROBLEM
An environmental services company working at a stainless-steel production facility faced constant issues with safety, compliance, equipment and meeting project deadlines. The mill, which was located in the Southeastern part of the United States, inevitably began searching for a more competent organization to manage its waste services, environmental spills and emergency response.
The new contractor would immediately need to improve processes including safety, efficiency and communication, in addition to offering consistent, flat-rate weekly invoicing with flexible pricing.
SOLUTION
In a joint venture between its industrial cleaning and environmental teams, MPW afforded the steel company the optimum combination of safety focus, expertise of personnel and quality of equipment. Consequently, MPW received a five-year contract from the customer.
MPW boosted the value of its services compared to the previous environmental contractor, adding industrial cleaning to the standard scope of work. A minimum of six full-time MPW employees (but up to 25 depending upon customer needs) and cutting-edge support equipment are now on-site every day.
Using processes and equipment that are more advanced than those of its predecessors, MPW manages and coordinates waste shipments, drum management – which consists of weekly inspections, consolidation and shipment coordination – and environmental compliance.
MPW’s execution of services has been spot-on since Day 1 at this location. Efficient work and effective communication with mill personnel have allowed MPW to handle projects not traditionally completed by environmental contractors.
RESULTS
MPW offered the customer long-term savings with weekly invoicing to sync with the customer’s budget.
The experience and leadership of MPW’s superintendent and project manager at the site have allowed for the implementation of best practices that have produced improvements in safety standards, compliance, organization and cleanliness.
Additionally, MPW coordinates its crews for ideal flexibility and proficiency, which has produced faster mobilization and movement from task to task.
As MPW continues to expand its relationships throughout the facility, it has received multiple glowing remarks from the client on Job Performance Evaluations (JPEs). Examples include:
“MPW was given the entire plant to service environmental issues. Our plant consists of four large mills and we employ nearly 1,500 people, so it’s a rather large task. They did a great job from the first day. Overall performance: exceeded expectations.”
– Administrative Personnel
“MPW’s Environmental Director of Operations is excellent.”
– Management Personnel
“The Area Sales Manager was diligent in continuing to ask for opportunities at our facility. He was persistent but not overly pushy. As the opportunities opened up, his coordination with other MPW personnel on quoting and learning all that he could on the scope of work was phenomenal. Follow this up with a great team of operations personnel and the overall picture of MPW at our site has been exemplary. Overall performance: exceeded expectations.” – Procurement Personnel